One of the nice things about building a boat is learning all the nautical terms for the bits and pieces. I must admit to be pretty clued up anyway, but I never really understood what was meant by the garboard. Now I know – it’s the next strake up from the sole.

This is where the beauty of CNC kits comes in – just by dry fitting the strake showed that everything was going to go together very neatly, with minimal fettling.
The joint between the sole and garboard is basically a butt joint, held together by stitch and glue. This is because the sole is thicker plywood than the garboard, so there’s a step at the joint. I remember the technique from when the Mirror dinghy was introduced, as it was basically used throughout. In practice the fit is so good, you can probably get away without stitching, as the joint is going to be taped afterwards. But orders is orders, so I tooled up with a handy gadget which I think was designed for fencing, but actually worked well in pulling the joint together.
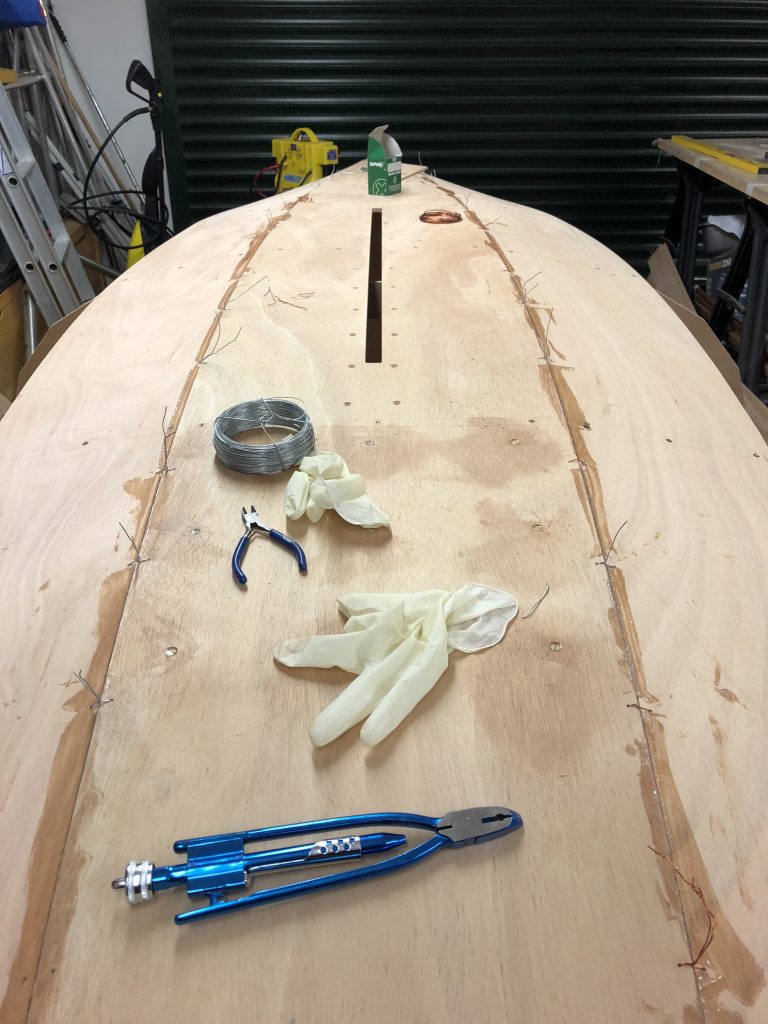
The curve at the forward end of the strake is quite daunting, but it was not difficult to get it all screwed and glued to the inner stem with sacrificial screws.
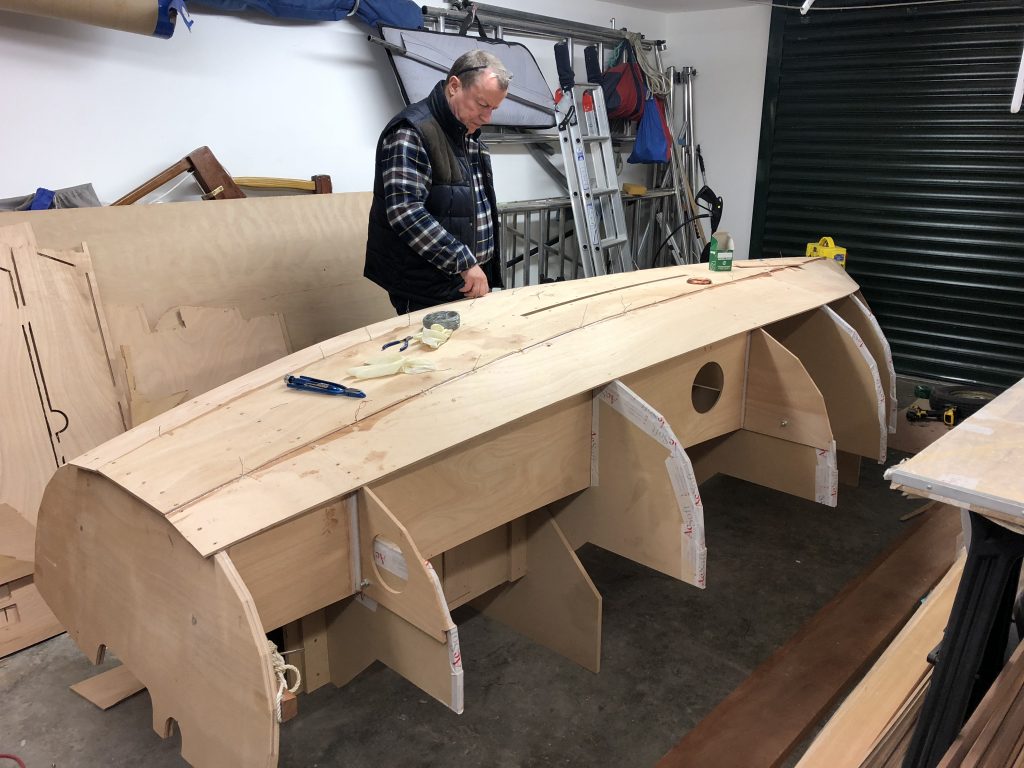
The strake can be screwed to each frame temporarily, but if I was building a varnished version, I might think of a better way of holding it all in place as per the Oughtred book.
Once the strake is glued to the longitudinal bulkheads, add some epoxy fillets on the inside of what will be the buoyancy tanks. It’s also worth getting underneath and wiping away any dribbles with acetone, otherwise it adds to the sanding work later on.
Now seemed a good time to drill and countersink the holes for the centreboard case log, otherwise that could be tricky once the hull is inverted.